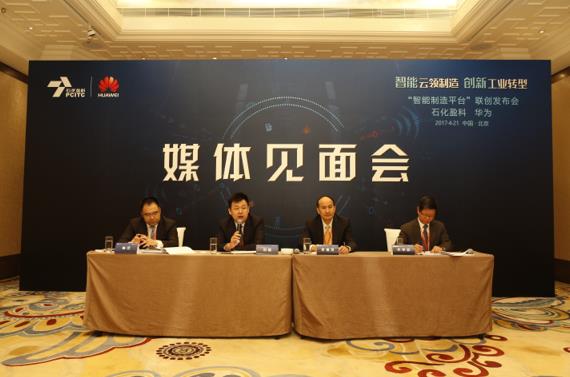
4月21日,华为联合石化盈科共同推出了面向石化行业的智能制造平台。
这是石化盈科与华为签约战略合作之后,双方进一步深入合作所取得的首个重要联合创新成果,也是石化智能工厂2.0建设的核心内容,全面体现了集中集成、物联网接入、IT管控、优化、共享服务、数据处理与分析、人工智能等八项核心能力,未来将会成为流程工业智能制造的“操作系统标准”。这也是站在行业、国家的高度,推进信息化和工业化深度融合,实施制造强国战略的重要举措。
就此,记者采访了中国石化集团信息化管理部主任、石化盈科董事长李德芳,石化盈科行政总裁齐学忠和华为企业BG中国区副总裁刘超、华为企业BG中国区大企业业务部部长姚茳。
记者:此次双方合作产生的契机是什么?未来准备在哪些领域开展深入合作?
刘超:其实,华为跟石化盈科的合作已经有比较长的历史了,并不是从去年才开始的。早在2012年,华为就和石化盈科对智能制造工厂一期试点的规划、技术选型工作进行了探讨。其中,华为实施的九江石化智能制造项目是炼化企业的模范标杆项目,参加了上海工业博览会,得到了工信部非常高的评价。
同时,因为石化盈科是中石化系统里信息化建设的关键角色,华为也是中石化多年ICT基础设施的供应商,在石化行业里有着丰富的积累和经验。基于历史上共同对于客户的价值,我们构建了战略合作的基础,联合推进智能工厂2.0版本。我们探讨了更新的ICT技术,进入到了企业的平台建设。我们的目标是实现炼化企业的自动化、数字化、可视化、集成化。以这几个标准来定义智能化的制造平台,也就是我们今天发布的平台。
记者:双方通过这个平台的合作想达到什么样的阶段性效果?要达到这样的效果还需要多长时间?
齐学忠:中石化的信息化过程已经有30年了。前20年,我们基本是跟着别人走,而且主体的软件都是进口的。但是30年以后,如果我们再走这条路,像中石化这样规模的企业可能越来越不可持续,尤其是能源行业是国家的一个自主产业。
中石化企业层面的基础设施、云平台都是由华为提供的。引入这个系统之后,所有管理人员到任何一个地方都可以借助手机看到装置的运行情况。这在以前是做不到的。
我们借助双方的合作,借助中国石化30年的积累,我们形成一个平台来承载所有企业的应用,实现从实践往理论方面的跨越。我们做这个也有理论支撑,形成了一个平台和技术、标准两个体系。同时,企业管理内容很多,生产内容也很多,如果把所有内容都放进来可能不行。所以,我们围绕生产过程一体化,从原料进厂到加工再到成品。
第二,将智慧过程的优化作为重点,比如,原料怎样以最少的投入,产生最多的产出。同时,对工厂里生产环节最重要的部分——设备怎样管理。
智能制造平台集成了DCS、PLC、RFID、手机终端、工业可穿戴设备、检测仪、分析仪等过程控制与装备,融合华为领先的ICT技术,依托智能化平台推出能源产耗在线优化、智能调度指挥、设备运行智能分析、安全环保智能监管等多个解决方案。方案以物联网、云平台、大数据为技术基础,以工作流、优化计算、知识库、报表服务、规则服务、日志服务等为技术手段,提供调度、预警、工厂监控、生产预测等多项业务服务,从而提升石化企业建设全面感知、优化协同、预测预警、科学决策的智能生产运营能力,支撑企业生产运行实现在线控制智能化、生产过程可视化、管理控制一体化、运行状态最优化。
记者:与其它行业相比,石油石化在推进智能化的过程中有哪些独特的地方?
姚茳:石油石化是典型的制造行业,尤其油气本身具有易燃、易爆的特点。这些产品对于安全性和可靠性的要求比一般行业要高,所以如何保持生产的安全性对于企业的生产效率和生产运营具有非常重要的意义。所以,在石油石化的智能制造推进过程中,要把稳定、安全放在首位。这些特点反映到ICT的能力,需要华为提供实时的通讯能力、实时的计算能力以及整体架构的安全能力。
未来的发展趋势就是集中化、智能化。只有通过先进的ICT技术才能驱动我们向未来的智能制造转型,才能实现我们在中国制造2025描述的制造企业的宏伟蓝图。我们跟石化盈科的合作,能够深入了解流程行业的业务特点,把我们产品的能力转化成客户的业务能力。
记者:中石化在智能制造领域的起步较早,已经走在行业前列。具体来说,中石化在智能制造方面取得了哪些进展?
李德芳:中石化是在2011年提出转型升级,像智能石化、智能油气田、智能炼厂、智能管网等。2011年,在国家智能制造2025还没有提出的时候,我们就开始对石化产业转型升级、提质增效做规划了。2013年具体实施,对镇海炼化、九江石化、茂名石化、燕山石化进行试点,经过3年的建设,打造1.0版本。通过试点,这4家企业的劳动生产率提高了10%,数字化自动采集率都在90%以上。我们装置了先进过程控制ADC,也在90%。另外,对于安全、环保水平的提升,包括能源的优化、大数据的应用、预测预警、设备的预知性维护,都取得了比较好的成果。九江石化、镇海炼化分别被列入国家的智能制造示范企业。
在智能油田方面,虽然规划做得比较早,但是从2016年才开始启动,相对较晚,走得也比较慢。现在油田数字化、自动化后,劳动生产率提高了50%以上。
2014年,根据国家的要求,为了提高安全、环保水平,中石化还规划建设了智能管线系统,覆盖了中石化5万多公里的长输管线,全部实现了数字化、网络化的管理,对于管线的周边情况、运行情况都可以做到实时动态的监控管理,大大提高了管线的安全管理水平。
下一步,我们将加大智能油气田的力度,加快推广智能工厂,提升、完善智能管线。
记者:智能工厂建设对于中国制造2025的实现有哪些作用?
李德芳:智能工厂建设是中石化自身发展的一个急迫需求。因为中石化面临着转型升级、成本、中低端产品过剩、安全环保等压力,所以我们要打造卓越、追求卓越、安全环保、劳动生产力高、质量高的工程。通过实践来看,安全符合中国制造2025的指导思想和要求。
中石化前几年在智能工厂的具体实践、试点,应该说不光是为中石化的产业转型升级提供了相关的理论、平台、经验和方法论,还有助于中石化智能制造、产业升级的发展,为发展中国制造2025提供了有益的经验和途径。
中石化取得的成果,探索的方法理论和经验,可以为其他行业、单位提供相关的经验和相关的技术、做法,包括下一步走出去,“一带一路”,结合我们的设计、工艺、技术创新,装备制造业的发展还会有很好的途径。我觉得这个方面的意义更大。
记者:您觉得在石化行业的转型升级中,面临的最大挑战是什么?应对措施又是什么?
李德芳:几十年来,中国石化产业的发展确实很快,满足了中国广大老百姓日常衣食住行的需求。但是高端、高附加值的产品还比较少。所以,我们的石化工业是大而不强,大而不优。此外,中国的炼油产能过剩约30%。这些都需要改革。
我认为对于工厂的安全环保能力的管控要提升。现在,很多石化工厂离城市很近,而现在城市扩大很快,有的甚至已经被城市包围。我们对于安全环保的要求越来越高。这是一个问题。
再一个,中国人工成本提高以后,劳动生产力、劳动效率也要进一步提高,怎样才能降本增效?还有供需问题、安全环保问题、产能过剩问题、劳动生产率提高的问题。我感觉这块不光要在管理上、技术创新上、装备上、改造上下功夫。
这些方面的创新改革升级都离不开ICT,新一代的新兴技术要和业务管理、技术创新、装备制造业的创新发展结合起来。要把我们现在面临的问题好好梳理一下。
实现的重要途径之一是打造新动能,就是利用物联网、大数据、云计算、新一代移动技术,包括人工智能,和我们工厂的装备、工艺、技术、管理等等结合起来,形成新的生产运营关键模式,形成我们新的对于设备的管控,对于安全的管控,对于流程的优化,来提高劳动生产率,降低成本,提高安全环保的管控水平。这是我们工业升级、新旧动能转换的一个有效途径。